Composite Panels
27th November 2017
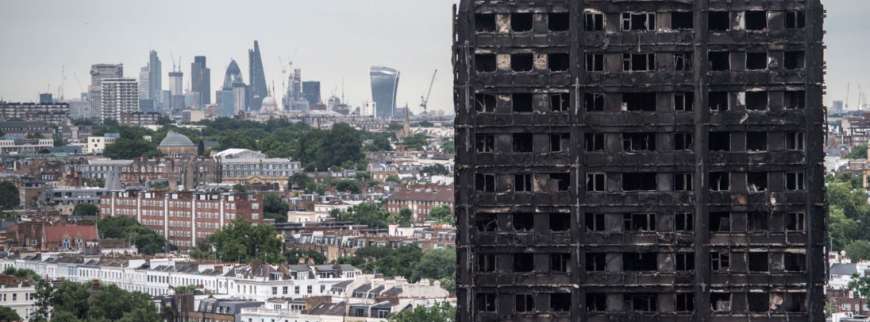
Composite panels are an insulated core bonded between two thin metal outer sheets. They are prefabricated, quick to manufacture, highly insulated, easy to clean and have been used in a variety of settings, from external cladding to internal party walls. They were originally used in light commercial settings involved in food manufacture where surfaces needed to be cleaned regularly and have been used more recently in the residential setting.
They can also have cladding materials added to the outside (scree and stone effect), which makes their presence hard to identify to the untrained eye. Any large smooth external area on a modern building is likely have some kind composite panel underneath.
Panel Types
There is a variety of different types of panel in use, made by a variety of manufacturers. All are rated for combustibility and fire spread.
Bonded sandwich panels – include metal faced insulated panels, bonded panels, composite panels and large insulated sandwich panels. These panels typically consist of a central insulation core sandwiched between an inner core and an outer metal skin. Common insulants include: polyurethane, polyisocyanurate and mineral wool based products. The outer metal skin can be PVC coated, for decorative or hygienic (wash-down) purposes.
Cladding panels – these panels are usually used externally and are now common in residential buildings. Also known as composite-cladding panels, external cladding panels and built-up cladding systems. Cladding panels can be bonded sandwich panels and there may be an air gap between the inner and outer surfaces. The central core can be covered by a layer of aluminium foil, glass tissue or similar material. The insulation materials in built-up systems are generally glass or stone wool, but may also be polyurethane based.
Polystyrenes (EPS) – these materials are thermoplastic in nature and generally melt and shrink away from the heat before ignition. This causes voids and reduces the structural strength of the panels.
Polyurethane (PUR) – these materials are exposed to heat during the manufacturing process meaning the rigid foam will tend to char when heated. At best, when used in a steel faced sandwich panel, the foam will char under the heat of an internal fire, but will remain structurally self-supporting. At worst, they will ignite as a result of flame penetration. Once ignited, the self-adhesive steel of the steel facings may fail and if the joints cannot support the weight, the facing may fall away.
Polyisocyanrate (PIR) – these materials usually char when exposed to ignition. PIR panels can emit decomposition gases in an explosive manner through whatever ventilation points they can find. This may produce jets of flames, or more rarely, a build-up of gases may force the facings away from the foam which then ignite.
Phenolic foam – generally, this material darkens in colour on heating, then forms a char and an ash. Some gases are released at the joints.
Mineral wool – this material tends not to play a part in the fire process, other than it retains heat. If the joints are penetrated, the core will smoulder but remains in situ. Where adhesives have been used between the facings and the core, small flames can sometimes be seen issuing from the joints. Although mineral wool type panels are the favoured material on account of the above, due to their density, weight and cost, they are not the builder’s preferred material.
Composite material panels – we are aware of research linked to the aircraft industry being undertaken into hybrid composite materials for use in panels which would make the fire proof.
The fire issue is that most types of foam insulation are relatively hard to ignite. However, once ignited there is a range of severity: at best, with the heat source removed they go out; and at worst, they burn readily, emitting thick dense black, toxic smoke and in some cases emitting deadly hydrogen cyanide gas.
Installation:
The installation of panels will have been pre-approved in the work specification and contract details of any construction or refurbishment project and once complete will have received sign-off for building regulation compliance.
The issue is that although standards have been adhered to and sign-off has been received, there is still a danger that the panels could be a danger in certain circumstances.
Losses related to panels:
Most panels will ignite eventually given enough heat or an accelerating circumstances and the fact that the panels can, in certain circumstances, exacerbate fires has been well known in the insurance industry for decades.
The Summerlands Holiday Park fire in the Isle of Man in 1973 which tragically caused 50 fatalities involved panels at the newly built leisure centre and the 2007 food packaging warehouse fire at Atherstone on-Stour tragically killed four firefighters also involved composite panels.
More recently there was the Lakanal House fire in Camberwell in 2009 and The Address hotel fire in Dubai in 2015 which both displayed external burning and a “chimney” effect. Other similar losses have been reported from around the globe.
In 2003 The Chartered Institute of Loss Adjusters (CILA) issued a technical bulletin which stated:
Probably over 90% of all composite clad buildings fall below insurers’ / reinsurers’ currently desired specification. The result being that the insurance market has hardened insurance rates, increased deductibles and treats some property as “uninsurable at any price”. Food processing and storage plants have been the focus of attention but many other buildings contain composite panels”.
Recommendations:
- We suggest that landlords and / or managing agents produce a register of properties that contain composite panels.
- Original build documentation / building regulation sign off / fire safety sign off should be gathered for those buildings with composite panels.
- Where this information is not readily available the original developer / original builder / developer / buildings control should be approached for this information.
- If this information is still not available, or where panels are identified, a cladding expert could be employed to review the materials used and to provide expert advice.
- Invasive sampling could take place to identify the type of panelling used.
- If the presence of highly combustible panels, or coverings with a highly likelihood of fire spread, are identified, the landlord / managing agent should consider what actions to take next. These could involve: removing and replacing the panels; installing additional fire stops; installing retrofit internal and/or external sprinkler systems; liaising with the fire authorities over evacuation plans; removing / relocating potential sources of ignition (ie bin stores).
- As a material fact, once panels are identified, this should be notified to insurers. Planned or completed remedial action would also help mitigate any premium increases.